Potash Mining Methods
Conventional Underground Mining
1. Service Shaft:
Shaft mines in Saskatchewan are approximately 1,000 metres below ground level. Shafts are used to move miners and equipment from ground level to the underground site.
2. Mining Machines:
Potash is mined using two and four rotor continuous boring machines. They can mine up to 900 tonnes per hour, making paths of up to 7.9 metres wide and 3.7 metres high.
3. Ore Storage:
Conveyor belts carry ore to underground bins where it is stored until it is transported to the loading pocket of the shaft hoist.
4. Production Shaft:
Potash ore is hoisted to the surface in ore skips that can hold up to 45 tonnes. The hoist consists of four headropes with one skip per side. While one unloads on the surface, the other one is loaded with ore at the bottom.
5. Process Plant:
A process plant separates the salt from the potash and converts the potash to the final product, ready for storage & shipping.
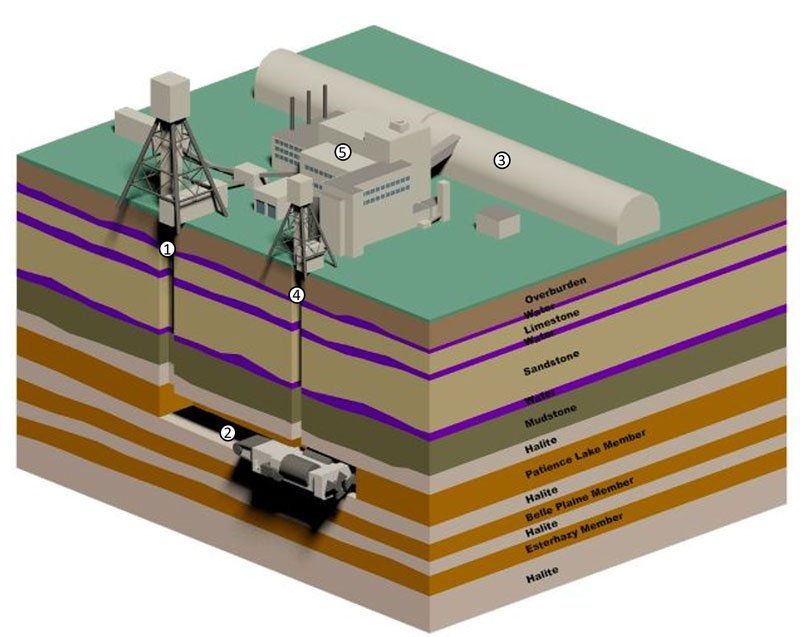
Conventional Solution Mining
After evaluating the alternatives from economic, engineering and operation perspectives, we believe that a solution greenfield potash project makes more sense than a conventional underground mine, as the reduced construction costs and time to construction allow a solution project to be first out of the gate, thus improving potash economics capturing the opportunity of Chinese coming “3 – 1/3 Strategy”.
1. Injection Wells:
Brine is injected underground and is circulated throughout the mine.
2. Dissolving:
The potash and salt is dissolved in the brine.
3. Extraction:
The solution is then returned to the surface and the potash is separated and conditioned.
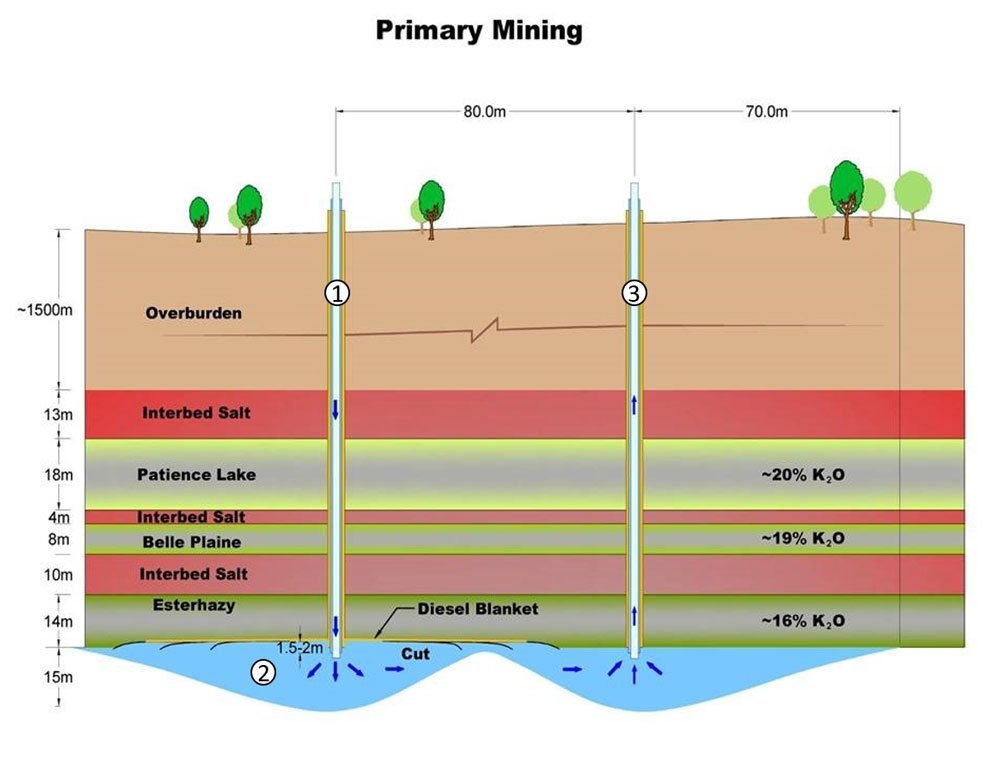
The Benefits of Solution Mining
Lower construction cost and shorter construction phase
The average capital expenditures for a solution mine is US$1,000/tonne, whereas an underground mine’s is US$1,400/tonne. Net asset value (NAV) for a solution mine surpasses that of a conventional underground mine at various potash prices. As BHP’s Jansen production and Chinese venture production in Lao merge to the market in 2015, China will have more bargaining chips with potash cartels such as Canpotax and BPC. It is likely to see the market price of potash to drop from the current $450/ton mark. Thus, a solution mine will provide a better hedge from the volatility of potash price.
Another advantage of solution potash projects is that the lead-time is two to three years less than that of conventional underground mines. The offset of this is its operating costs, which incurs typically 20%-30% higher over conventional mining. However, the two to three year leading time will be more corresponding to China’s 2010- 2015 “Five Year Plan” time frame.
Lower break-even price point and higher IRR
We estimate that the break-even potash price for a solution mine is US$200/t and for a conventional underground mine US$235/t. A Saskatchewan Greenfield potash mine requires a potash price of US$435/t to earn a 15% internal rate of return (IRR) for solution mining and US$580/t for a conventional underground mine.
Lower engineering risk and higher extract ratio
Solution mining of potash offers reduced engineering risk compared to conventional underground mining due to the flexibility of the location of the extraction well versus conventional mining, which is tied to one location for ore removal. In solution mining, a number of internal and external wells are drilled, with an estimated 40 caverns required for a 2 million tonne/year mine (one cavern represents two holes). Consequently, solution mining offers the ability to move operations to other locals [e.g. to avoid geological anomalies like a”salt horst” (a salt horst is pockets, lenses, irregular beds, or channel fills that contain salt, a non-potash containing ore, within the ore bed)] for a much lower capital cost (as compared to conventional potash underground mining techniques).
Lower human capital requirement but higher energy consumption
Of the 11 potash mines in Saskatchewan, nine are conventional underground mining operations, which require underground equipment and personnel. The other two are solution mines, which involve pumping heated water through the ore body to dissolve the potash and pumping the resultant brine solution to a refinery for extraction. Solution mining is a more energy intensive process than conventional mining. Comparing 11 potash mines in Saskatchewan, solution mining’s average energy consumption was about 1300kWh/tonne and conventional mining’s was close to 400kWh/tonne. Natural gas represents the largest source of energy type for the Canadian potash industry, representing almost 80 percent of total energy consumed annually. Electricity makes up about 20 percent of the energy consumption on a total MWh basis. The remainder of the energy consumed is in the form of diesel, propane, gasoline or fuel oil.